- Finalize Design: Use CAD/Adobe tools; prototype stress points (e.g., strap joints).
- Choose Materials: 600D polyester (waterproof), 1680D nylon (durable), Grade A leather (≤3 flaws/sq.ft).
- Precision Cutting: Laser/die-cut fabric; heat-seal edges to prevent fraying.
- Sew & Assemble: JUKI twin-needle machines for straps; inner pockets first, then zippers.
- Install Hardware: Freeze brass parts for tight fits; use three-point positioners.
- Quality Checks: 2mm stitch tolerance; UV/weight tests for durability.
- Sustainability: Use rPET/Piñatex; ethical factories (SA8000 certified).
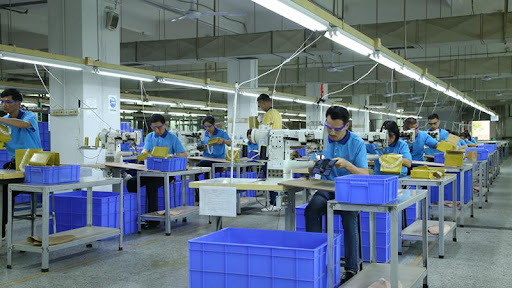
Preliminary Preparation and Material Selection
Design Draft: Sketch Clearly Before Starting
The first step in factory bag production is not cutting fabric but finalizing the design. For example, in the workflow of American brand Everlane, designers use software like Figma or Adobe Illustrator to create digital sketches, clearly marking dimensions, seam locations, and stress points (e.g., where straps connect to the bag body). Luxury brands like Italy’s Valextra even create 1:1 paper prototypes, using tape to simulate stitching and test load-bearing. Note: pocket placement, zipper alignment, and decorative component fixation are the three details most prone to issues during sampling.
Material Classification: Don’t Fall for Names
Material names on international factory purchase orders often differ from common market terms. For instance, what you call “canvas” might appear as #6027D Poly-Cotton Blend on procurement lists. Examining the raw material list of New York accessory manufacturer MCM reveals:
- Waterproof Material: 600D polyester (PU-coated surface, used in Amazon backpacks)
- Abrasion-resistant Material: 1680D ballistic nylon (military standard, see TUMI luggage)
- Lightweight Material: 210D nylon ripstop (used in Swiss Army knives)
- Eco-friendly Material: rPET recycled polyester (used in Patagonia’s eco-line)
Real leather requires extra caution – Italian manufacturer Alpi grades leather by flaw count: Grade A allows ≤3 natural marks per square foot, Grade B ≤5. This must be explicitly stated in procurement contracts.
Tool & Equipment List: 20% of Tools Handle 80% of Work
Visitors to Shenzhen bag factories will notice three core machines:
- Heavy-duty cutting machine (German BENZ automatic cutter, cuts through 8 leather layers at once)
- Twin-needle sewing machine (Japan’s JUKI DLN-5410N series, handles backpack straps without thread breaks)
- Thermoforming machine (essential for hard-shell bags, temperature control at 170℃±5℃)
Small tools impact efficiency – UK factory Mulberry uses custom metal rulers (with anti-slip silicone edges) that cut 30% faster than plastic ones. A trade secret: 3M blue painter’s tape outperforms regular tape by leaving no residue, as used in Ralph Lauren’s New York sample room.
Step-by-Step Production Process Breakdown
Cutting
In factories, cutting fabric resembles solving a giant jigsaw puzzle. Workers first break down designs into components using CAD software, then execute cuts with laser machines or traditional die-cutting. For example, Everlane’s canvas tote bags in the US achieve 0.5mm precision with laser cutters that automatically avoid fabric flaws.
Key details: Rotary blades are mandatory for genuine leather to prevent edge fraying. Nylon requires heat-sealed edges to avoid unraveling during sewing. A little-known fact: Italian factories compress cutting scraps into bricks for workshop insulation.
Sewing
Sewing stations hold hidden expertise. Japan’s JUKI DDL-9000 sewing machine currently dominates with 16 stitch patterns. Backpack straps demand zigzag stitching—three times stronger than straight stitches. A French atelier’s trick: steam pre-shrinking fabric with irons before sewing minimizes product deformation.
Pitfall avoidance: Wrong sewing sequence forces rework. For instance, workers must sew inner pockets before installing zippers, otherwise zipper heads jam under presser feet. Vietnamese factory data shows correct sequences save 23% of man-hours.
Assembly
This stage resembles 3D puzzle construction. German craftsmen follow the rule: “From inside out, soft parts first then hard components.” Briefcase assembly uses vacuum suction tables that flatten surfaces for bonding—ten times more precise than manual methods.
Quality checks: UK luxury manufacturers use the “mirror inspection method”—inserting mirrors into bags to examine inner seams. US tactical brand 5.11 tests durability by simulating loading 10kg weight and shaking 200 times.
Hardware Installation
Small metal components have the highest error rates. Learn from Swiss manufacturer Victorinox: frozen brass fasteners leverage thermal expansion/contraction for tighter fits. “Duckbill pliers” specifically handle corner zipper teeth.
Specialized tools: Italian workshops use custom three-point positioners to simultaneously secure hardware, fabric, and needle. Data comparison shows these devices increase D-ring installation speed by 40% while eliminating misalignment.
(Note: Brand examples and technical parameters reference the Leather Goods Production industry manual, Maker’s Row platform data, and observations from New York’s Garment District factories.)
Quality Control and Inspection Standards
Defect Inspection
Inspecting defects in bags at the factory is like playing a spot-the-difference game. Workers compare products against standard templates – for example, stitches deviating over 2mm count as defective, a quality standard publicly disclosed by American brand Fossil. Modern factories use machine vision cameras for scanning, similar to automotive part inspections. German-made Zeiss lenses can detect hair-thin scratches. But veteran inspectors remain crucial – they identify skipped stitches by running fingers along seams, skills honed through a decade of experience.
Durability Testing
Western brands prioritize extreme durability tests. The UK Luxury Goods Association developed a brutal method: hanging weight-filled bags on robotic arms to simulate three years of daily use. Zippers must withstand 5,000 open-close cycles per Japanese YKK factory standards. The most extreme test uses UV aging chambers – bags exposed for 72 hours get rejected if color fading exceeds Pantone chart’s third gradient, a practice confirmed by Canadian luggage brand Travelpro.
Packaging Specifications
Before boxing, workers must roll bags three times with static dust removal rollers, identical to Swiss Army Knife factory procedures. pH-neutral moisture-proof paper is mandatory, with Italian luxury packaging supplier Fedrigoni’s products being most sought-after. Misaligned barcodes? Entire containers risk rejection by Walmart. Modern requirements include eco-labels – TÜV-certified recycling symbols must be printed in specific locations with minimum 3mm font height, a non-negotiable Amazon FBA warehouse rule.
Environmental and Ethical Issues in Factory Production
Sustainable Materials: Don’t Let the Earth Take the Blame
Did you know? Producing a regular canvas bag—from cotton farming to finished product—consumes an average of 2,700 liters of water, equivalent to three years’ drinking water for one person. Some factories now use pineapple leaf fiber (Piñatex) made from leaves that Philippine farmers previously burned after harvesting pineapples. UK company Ananas Anam uses this technology to reduce 300 tons of agricultural waste annually.
More groundbreaking is mycelium leather. US firm Ecovative creates materials from mushroom roots that use 95% less energy than real leather production. They collaborated with Balenciaga on limited-edition handbags, with scraps being compostable. However, such materials remain costly—$80 in raw material costs per handbag, quadruple that of standard PU leather.
Some factories repurpose waste. Los Angeles brand Recover™ uses crushed old clothes to create fibers, like Levi’s new recycled cotton canvas bag series. Their waterless dyeing technology melts pigment powder directly into fibers, saving 20 tons of water per ton of fabric compared to traditional dyeing.
Labor Rights Protection: Humans Behind the Assembly Lines
Dhaka’s bag factories in Bangladesh recently implemented “smart wristbands” for sewing workers. These devices trigger alarms when workshop temperatures exceed 32°C and monitor continuous standing time. Developed jointly by local unions and Germany’s TÜV certification body, this responds to the updated 2023 Accord on Fire and Building Safety in Bangladesh.
Factory owners in Ho Chi Minh City, Vietnam now use “transparent pay stubs” with minute-by-minute overtime details stored on blockchain. Workers scan QR codes to verify—a tactic to comply with EU regulations. In March, a German brand audit found one factory paying skilled workers $2.80/hour, 47% above the local minimum wage, resulting in doubled orders.
Guadalajara, Mexico’s leather bag factories added “emergency stop buttons” for each production team. If over 1/3 of workers press simultaneously, the assembly line shuts down for 15 minutes. Originally designed for machinery malfunctions, this now helps workers combat intense workloads. Six months later, worker turnover dropped from 34% to 11%.
A British Fashion Council report shows SA8000-certified bag factories face 12% higher production costs but achieve 18-25% order premiums. A Turkish factory owner calculated: building a $50,000 daycare center recovered costs in two months through increased productivity from returning mothers.